noodle-led
Well-Known Member
In 2016 I saw a Hackaday post about someone building their own grow light and I got excited about the prospect. Literally 2 google searches later I ended up here and was given more information about every aspect of LED grow lights than I ever thought I needed to know. Thanks for steering me away from grabbing some blurple LEDs and having a go at it! I've got a small tent with a couple Gen 7 Vero 29 cobs that does a pretty good job for the past year+, but the light is pretty uneven in there so I've been looking at alternatives.
The EB Gen 2s look good and their ~2ft size would make a pretty good fit for my 32x32" space. The questions I had were
Testing
One 3500K 560mm Bridgelux EB Gen 2 strip was purchased from Arrow with one of my recent parts buys. The strip was powered by soldering 2 inch 20AWG wires to the two terminals at the end of the strip, and fed with 18AWG wires from a bench power supply. The strip was elevated on 1.5" wooden blocks at either end and one in the center with the LEDs facing up, unless otherwise noted. The strips were left running and checked every 5 minutes until the forward voltage was the same across two checks. Ambient temperature was 19.1C, and as an extra data point, the strip at 1400mA fully cold tops out at 20.50Vf but drops very fast as it heats up. I checked each LED's thermals for each test, but every time I ended up with the same group of LEDs being the hottest on the whole strip.
First, the numbers in free air, no ambient airflow or heatsinking.
700mA 19.26Vf 43.4C
1050mA 19.68Vf 56.4C
1400mA 20.08Vf 71.9C
Note that these are not the best at thermal transfer to the back of the strips. The back of the 71.9C strip was more than 5C below the front of the strip
It is clear that at 700mA, Bridgelux's claims are true: no heatsinking required. Next I tried a variety of materials for heatsinking at 1400mA, all attached with 20mm thermal tape. 4" wide strips of flashing material were chosen as a common spacing for 24" installations with 6 strips.
Finally I ran a set of tests with the bare strips again at different currents to note the response of power to heat. What was very interesting was that there is a knee on the power vs temperature rise curve. I didn't believe it so I ran it twice and got the same results:
As a side note, I also turned on a fan in the room for one of the tests against the bare strip at 1400mA. The Vf climbed from 20.08V to 20.16V which indicates somewhere around a 5-10C drop in temperature. I did not record the temperature in my notebook for some reason though. Was alcohol involved?
Conclusions
In short, I am looking forward to Digikey and Arrow stocking more of these in different color temps. I'd prefer doing 5x 4000K strips and 4X 3000K strips with a switch to bypass and disable the 3000K while running them off the same driver for veg. Although maybe I am tipping my hand too much about my next build plans...
The EB Gen 2s look good and their ~2ft size would make a pretty good fit for my 32x32" space. The questions I had were
- How many should I use? My current setup is 2x COBs on 120mm pin heatsinks on a HLG-185H-C1050 running at just over 70W. They generate ~24800 theoretical lumens at ~176lm/watt with Ledil Angela 90 degree reflectors. I'd obviously want better than this so it was a good starting point.
- How hard can I drive the strips? U-channel or heatsinks can be used to keep the temps down, but 2ft for each strip x 10 strips, the costs gets out of hand, so the goal would be to maximize the output without causing failures and minimizing cost.
- How hot do they get? This is sort of related to the second point, but heat is largely related to reliability.
- How many strips on a driver? The datasheet says to model driver selection with a 22.1V/560mm strip Vf but that creates some sub-optimal breakpoints given the forward voltage for Mean Well drivers. HLG-240H-CXXXX can get 8x1.4A for only 217W or 10x1.05A for 204W. HLG-185H-CXXXX are 6x1.4A (162W) and 8x1.05A (162W). I wanted to see some real world numbers before committing to getting a new driver and strips.
Testing
One 3500K 560mm Bridgelux EB Gen 2 strip was purchased from Arrow with one of my recent parts buys. The strip was powered by soldering 2 inch 20AWG wires to the two terminals at the end of the strip, and fed with 18AWG wires from a bench power supply. The strip was elevated on 1.5" wooden blocks at either end and one in the center with the LEDs facing up, unless otherwise noted. The strips were left running and checked every 5 minutes until the forward voltage was the same across two checks. Ambient temperature was 19.1C, and as an extra data point, the strip at 1400mA fully cold tops out at 20.50Vf but drops very fast as it heats up. I checked each LED's thermals for each test, but every time I ended up with the same group of LEDs being the hottest on the whole strip.
First, the numbers in free air, no ambient airflow or heatsinking.
700mA 19.26Vf 43.4C

1050mA 19.68Vf 56.4C

1400mA 20.08Vf 71.9C

Note that these are not the best at thermal transfer to the back of the strips. The back of the 71.9C strip was more than 5C below the front of the strip
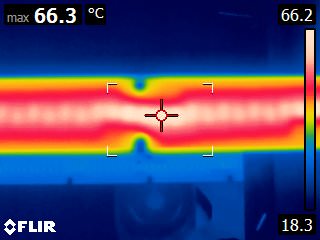
It is clear that at 700mA, Bridgelux's claims are true: no heatsinking required. Next I tried a variety of materials for heatsinking at 1400mA, all attached with 20mm thermal tape. 4" wide strips of flashing material were chosen as a common spacing for 24" installations with 6 strips.
Code:
1" wide x 1/8" aluminum bar -- 20.12Vf 67.0C
1/2"x1/2"x1/16" aluminum L bracket attached to the back center of the strip -- 20.13Vf 66.3C
1"x2"x1/16" aluminum tube, attached on the 1" side -- 20.22Vf 55.5C
4" wide strip of heavy duty Reynolds aluminum foil -- 20.11Vf 67.1C
4" wide strip of galvanized steel flashing -- 20.20Vf 56.4C
4" wide strip of aluminum flashing -- 20.21Vf 55.7C
Finally I ran a set of tests with the bare strips again at different currents to note the response of power to heat. What was very interesting was that there is a knee on the power vs temperature rise curve. I didn't believe it so I ran it twice and got the same results:

As a side note, I also turned on a fan in the room for one of the tests against the bare strip at 1400mA. The Vf climbed from 20.08V to 20.16V which indicates somewhere around a 5-10C drop in temperature. I did not record the temperature in my notebook for some reason though. Was alcohol involved?
Conclusions
- It seems the best efficiency considering output to power is somewhere around 1A, so a 1050mA driver is probably the sweet spot if you want to get the most out of these.
- If you're planning on driving at 700mA, don't waste any money on heatsinking.
- The lower than spec forward voltage is also a boon, meaning a HLG-185H-C1050 can drive 9 strips at 1050mA for 185W and a theoretical 32,400 lumens (175lm/W).
- Don't waste your money putting 1" wide 1/8" aluminum bar on on each strip, aluminum foil works just as well once the temperature reaches equilibrium. This is no surprise, you haven't increased the radiant surface area by adding a slab the size of the strip to the back.
- Galvanized steel is surprisingly good and cheap compared to the expensive tubular aluminum (which I will admit I heated with a heat gun to bring it to temperature and then let it cool to equilibrium, it was just taking too long to heat on its own). Aluminum flashing is probably the most economical solution to provide rigidity and cooling.
- Figure at worst a 20.5V forward voltage at 1400mA when considering drivers, or a 20V forward voltage for 1050mA
In short, I am looking forward to Digikey and Arrow stocking more of these in different color temps. I'd prefer doing 5x 4000K strips and 4X 3000K strips with a switch to bypass and disable the 3000K while running them off the same driver for veg. Although maybe I am tipping my hand too much about my next build plans...