cobshopgrow
Well-Known Member
?
what else do i say?
meanwell drivers are isolated, i know none which isnt, therefore grounding the frame give no benefit.
its not what youve said, you say you should ground your frame when using a isolated meanwell driver.
or as you wrote, can even cause problems, extra nosie grounding your dc side (the frame).
maybe link to what youve found.
here is another general explanation.
"Currently in the general LED lighting market, there is a non-isolated and isolated difference for driver powers. Non-isolated design is limited to double insulation products, such as light bulbs alternative products, including LED and the product are integrated and sealed in a non-conductive plastic, so the end user does not have any risk of electric shock. Products of Class II are isolated, the price is relatively expensive, but the user can access to the LED and output wiring place (usually applied in LED lighting and street lighting), this product is essential.
With isolation transformer or electrical isolation LED driver power supply means that the LED can be directly touched by hand without electric shock. Without isolation transformer, though it still can make use of protective shell to achieve some mechanical insulation, but this time the LED can not be in direct contact with when at work."
www.ledaplus.com
but best is really the first link i posted.
"With an isolated power supply, like any of the Mean Well LED drivers, I can take the wires meant for the LEDs and take them right to ground potential with no problems, no damage, and no current flow (it is the current that kills). This is a safety test I do with most everything I analyze if I'm actually digging in to a light fixture. Non-isolated means that the current would flow. "
he is comparing unisolated drivers in lightbulbs and compare it to isolated like the meanwells, he is of course refering to the ground potential comming out of your wall, AC side,as you do.
what else do i say?
meanwell drivers are isolated, i know none which isnt, therefore grounding the frame give no benefit.
its not what youve said, you say you should ground your frame when using a isolated meanwell driver.
or as you wrote, can even cause problems, extra nosie grounding your dc side (the frame).
maybe link to what youve found.
here is another general explanation.
"Currently in the general LED lighting market, there is a non-isolated and isolated difference for driver powers. Non-isolated design is limited to double insulation products, such as light bulbs alternative products, including LED and the product are integrated and sealed in a non-conductive plastic, so the end user does not have any risk of electric shock. Products of Class II are isolated, the price is relatively expensive, but the user can access to the LED and output wiring place (usually applied in LED lighting and street lighting), this product is essential.
With isolation transformer or electrical isolation LED driver power supply means that the LED can be directly touched by hand without electric shock. Without isolation transformer, though it still can make use of protective shell to achieve some mechanical insulation, but this time the LED can not be in direct contact with when at work."
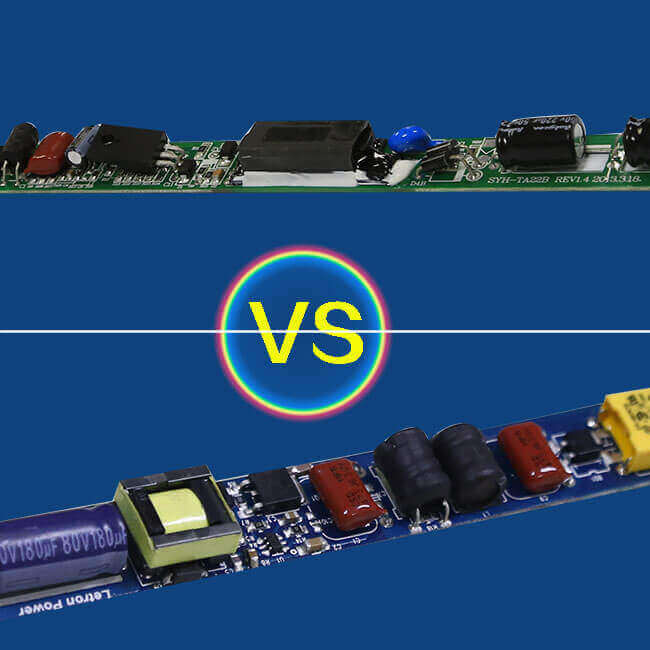
Isolated LED Driver Vs Non-isolated LED Driver | Architectural Lighting Developer & Manufacturer in China
Currently in the general LED lighting market, there is a non-isolated and isolated difference for driver powers. Non-isolated design is limited to double insulation products, such as light bulbs alternative products, including LED and the …

but best is really the first link i posted.
"With an isolated power supply, like any of the Mean Well LED drivers, I can take the wires meant for the LEDs and take them right to ground potential with no problems, no damage, and no current flow (it is the current that kills). This is a safety test I do with most everything I analyze if I'm actually digging in to a light fixture. Non-isolated means that the current would flow. "
he is comparing unisolated drivers in lightbulbs and compare it to isolated like the meanwells, he is of course refering to the ground potential comming out of your wall, AC side,as you do.
Last edited: